Waste from decommissioned electric vehicle lithium-ion batteries alone could total 4M tons annually by 2040, or nearly the weight of 22,000 Boeing 747s. Less than 5% of battery waste is recycled or repurposed, which means the remaining 95% causes environmental and resource problems. The unstable supply chain and depletion of mining resources further aggravate the problem. As a result, the market is driven to investigate lithium-ion battery recycling and reuse.
Enter Princeton New Energy
Princeton NuEnergy (PNE) (CleanTech Open National Winner 2021, 2022 applications due April 17th) uses a process developed by researchers who combined expertise from diverse fields to solve the problem of how to reuse lithium-ion batteries. PNE’s mission is to:
- Deliver a cost-efficient, environmentally friendly lithium-ion battery recycling solution
- Solve the current industry pain point of high-operational cost battery recycling
- Improve battery recycling efficiency and provide low-cost battery materials
- Reduce demand for minerals from overmined areas where environmental and labor issues are rampant
PNE turns spent cathode materials, the most expensive part of a lithium-ion battery, into pristine new cathodes. PNE recovers much of the structure and composition of the used cathode, along with the materials (cobalt and lithium).
PNE’s direct recycling process can recover up to 95% of all constituent materials compared to the methods currently used in the battery recycling industry. Additionally, comparing PNE’s technology with virgin materials from mining, PNE’s recycling technology results in 80% less CO2 emissions, 70% less water use, 80% less energy use, and lower gas and liquid waste.
The direct regeneration of cathode materials using PNE’s technology will increase the commercial viability of lithium-ion batteries and reduce battery cost, accelerating the electrification of transportation and large-scale energy storage.
How it Works
PNE has successfully developed a novel low-temperature plasma-assisted separation process (LPAS) that allows cathode materials to be sorted, purified, and regenerated. Additionally, it even adds new functionality to improve cathode materials’ performance. The technology enables the regeneration of cathode and anode materials without completely breaking down the chemical compounds, significantly reducing energy and chemical consumption.
The Competition
Current recycling practices, such as pyrometallurgy and hydrometallurgy, are energy-intensive and extremely inefficient at extracting metals from spent batteries. Pyrometallurgy, for example, has been commercialized because of its simplicity and efficiency in recovering cobalt and nickel. However, it is a process characterized by high energy consumption and high-cost equipment investment. Therefore, many hydrometallurgical techniques have been developed by various companies. This method is not as energy-intensive as pyrometallurgy, but its main challenge is the selectivity or selective recovery of different metals. During the process, other metals and ions may be dissolved, making the separation of the target materials difficult.
Another significant issue of hydrometallurgy is the strong dependence on pre-treatments. Current technologies for recycling lithium-ion batteries rely on harsh chemicals and high temperature, energy-intensive processes to break down spent batteries to their elemental components. These processes have been challenging to scale up commercially and make environmentally viable.
LPAS enables the production of high-quality battery materials at a low cost without using any acids. The technology will also shorten recycling time and costs while producing high-performance battery materials.
The Market
The market for battery recycling is projected to grow from $2B in 2021 to $27.3B in 2030, representing a CAGR of 33.8%. There are a couple of factors driving this.
Most spent batteries end up in landfills today because the industry lacks a clear path to large-scale economic recycling. As a result, battery researchers and manufacturers have traditionally not focused on improving recyclability but have concentrated their efforts on lowering costs, increasing battery longevity, and increasing charge capacity.
There are also currently around 465,000 tons of used electric vehicle batteries in need of processing today. That number will only grow. According to Princeton’s Net-Zero America study, reaching net-zero emissions by mid-century would mean the number of electric vehicles would increase from 1M on the road today to between 210-330M. Electric vehicle batteries have a lifetime of five to ten years, and there are about 3,000 battery cells per vehicle, depending on the model.
Outlook
The growing production of lithium-ion batteries has facilitated their inclusion in energy policy. Regulations are likely to play a key role in the future of lithium-ion battery recycling, which is vitally essential for the sector as it reduces resource scarcity and improves sustainability.
PNE’s LPAS technology is not only needed; it is also transformative. It can create new cathode materials from recycled batteries, establish U.S. leadership in manufacturing lithium-ion batteries, and protect the environment and human health.
The team hopes that in a couple of years, they can increase recycling capacity enough to launch from consumer electronics into electric vehicle batteries and perhaps even expand into whole battery manufacturing using their regenerated materials. Their goal is to grow their operations to a global total annual capacity of over 300,000 tons.
About The Author
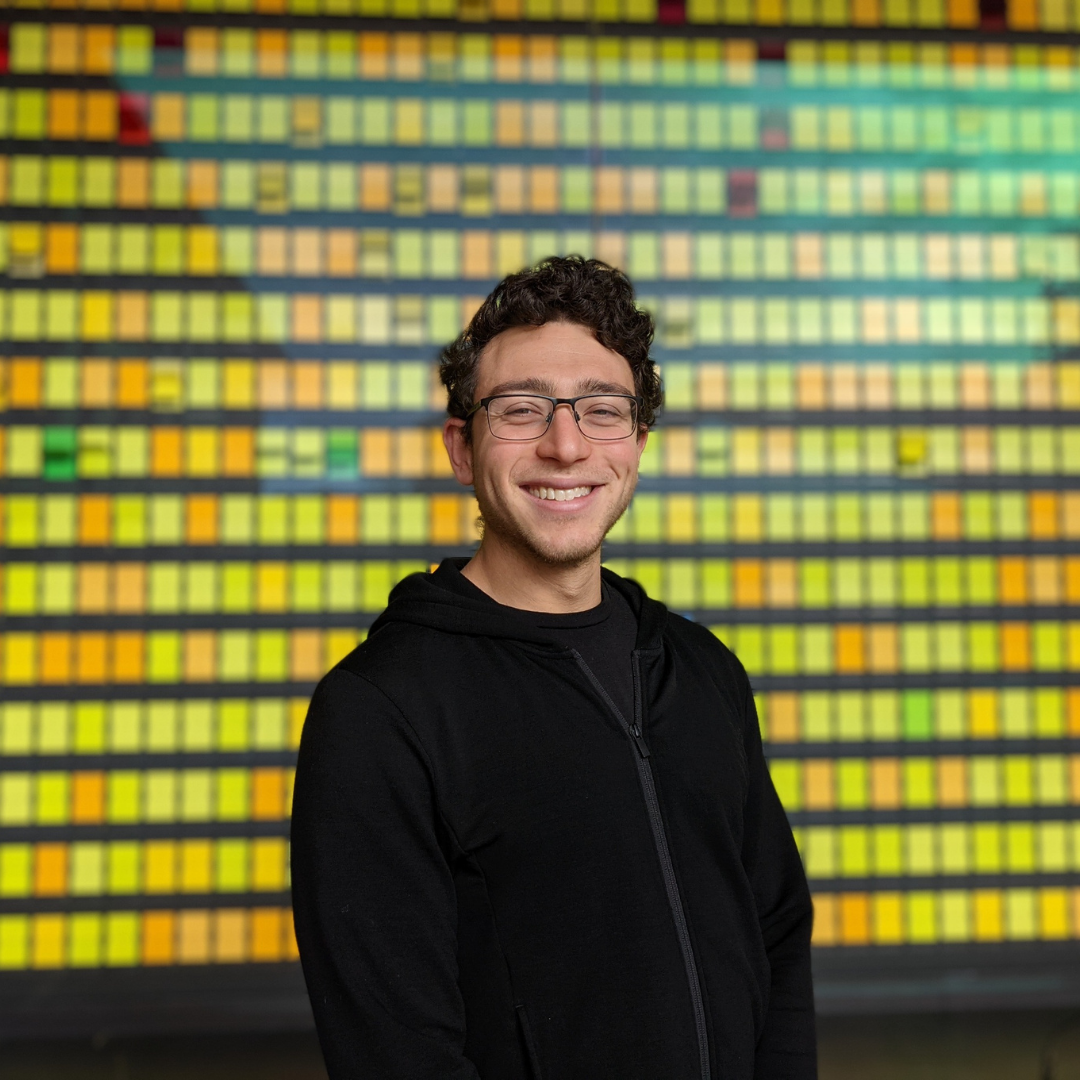
Daniel currently works at Lawrence Livermore National Laboratory as a Product Manager. Outside of his day job, he is a Principal at C3, Tech Scout at For ClimateTech, and Venture Scout at Prithvi. He also works with various climate incubators/accelerators (Cleantech Open, Techstars, and Joules Accelerator) and runs The Impact and Innovate Climate – both are newsletters covering startups in the climate space.